Extrusion
Advanced components for the extrusion industry
The extrusion industry requires materials and components that can cope with extremely difficult conditions. Having worked together with extrusion plants for more than 30 years, we have seen many problems and success stories and have definitely learned a lot. High quality and creative solutions stem from the combination of the experience at Uddeholm Machining and the highly qualified researchers and application engineers of our Uddeholm sister companies.
We design and produce extrusion components. These are often delivered as parts of a system, complete with heating and cooling systems, as well as an on-going service commitment. For example, when the extrusion container needs reconditioning, we carry out a service at our plant in Hagfors, Sweden. We also keep a log of our customers’ tools, making it easy to amass knowledge over time and monitor the customer’s tool and any servicing carried out. This is a service we know is valuable.
Let us be your partner in the never-ending search for highest performance and lowest cost per produced unit. Together we find the causes of any issue and advise you to appropriate countermeasures. In addition to advice, we also provide drawings, engineering support and components or systems.
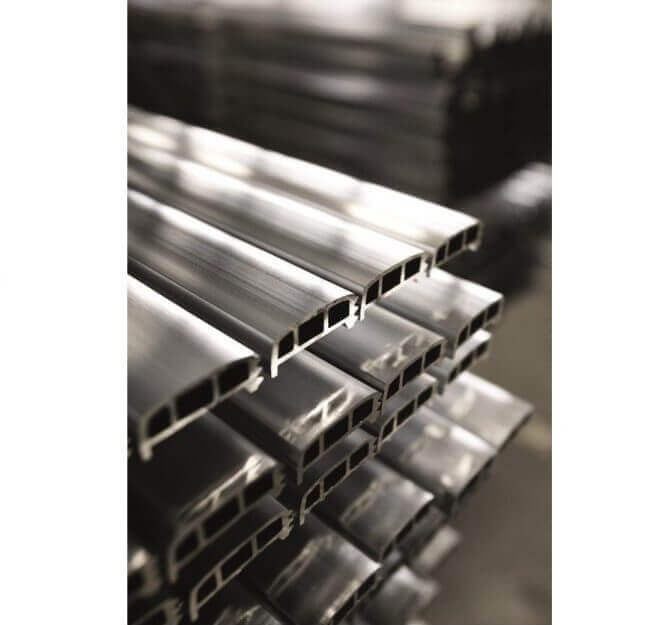