Teil 2 – Uddeholm Dievar
Pulver für die additive Fertigung
Haben Sie Teil 1 zum Thema Uddeholm Dievar – Pulver für die additive Fertigung / verpasst? Hier geht es zum Artikel.
Uddeholm Dievar ist ein etablierter Warmarbeitsstahl. Seine erstklassige Kombination aus Zähigkeit und Warmfestigkeit führt in vielen Fällen zu deutlich längeren Standzeiten. Seit einigen Jahren ist Dievar auch als Pulver für die additive Fertigung verfügbar. Das Zusammenspiel der Möglichkeiten der additiven Fertigung mit dem einzigartigen Eigenschaftsmix von Dievar kann zu deutlichen Produktivitätssteigerungen und Kosteneinsparungen im Druckgießprozess führen.
Uddeholm Dievar als erprobter Warmarbeitsstahl wird weltweit und vor allem für Druckgussformen eingesetzt. Er bietet eine herausragende Zähigkeit, Warmfestigkeit und Einhärtbarkeit. Insbesondere beim Gießen von Strukturteilen kommen die Vorteile dieses Eigenschaftsmix zum Tragen. Damit trägt der Trend zu gegossenen Strukturteilen aus Aluminium zum Erfolg von Dievar bei. Ein Meilenstein in der „Vita“ von Dievar war die Erhöhung der garantierten Kerbschlagbiegearbeit von 19 auf 25 Joule (Charpy-V Werte nach Lieferrichtlinie NADCA #207; „Capability“). Durch Optimierungen in der Stahlherstellung konnte die Zähigkeit insbesondere bei großen Abmessungen gesteigert werden.
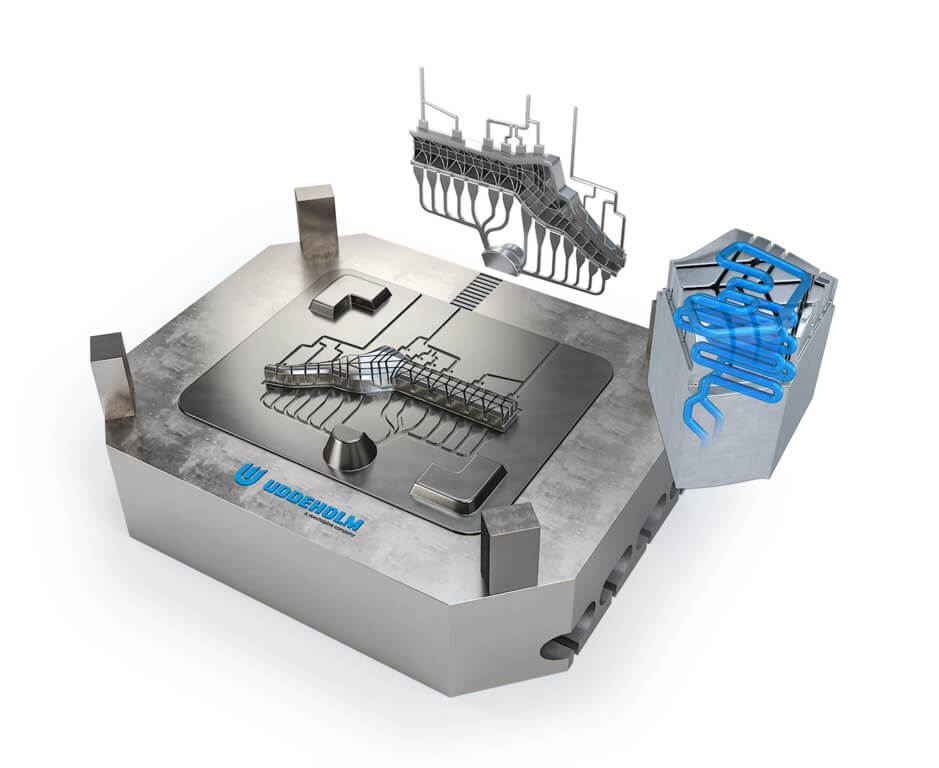
Diesen Vorteil geben wir an unsere Kunden durch erhöhte Garantien weiter. Damit nimmt Uddeholm Dievar eine einzigartige Stellung unter den Warmarbeitsstählen ein. Dieses wird unter anderem dadurch sichtbar, dass er in der Kategorie „Typ C1850“ in der NADCA #207 eingeordnet ist. In dieser Kategorie sind die Warmarbeitsstähle mit einer hohen Warmfestigkeit (2,0 – 3,3 Gew.-% Molybdän) und gleichzeitig hohen Zähigkeit (mindestens 25 Joule Kerbschlagbiegearbeit nach Lieferrichtlinie NADCA #207; „Capability“) aufgelistet.
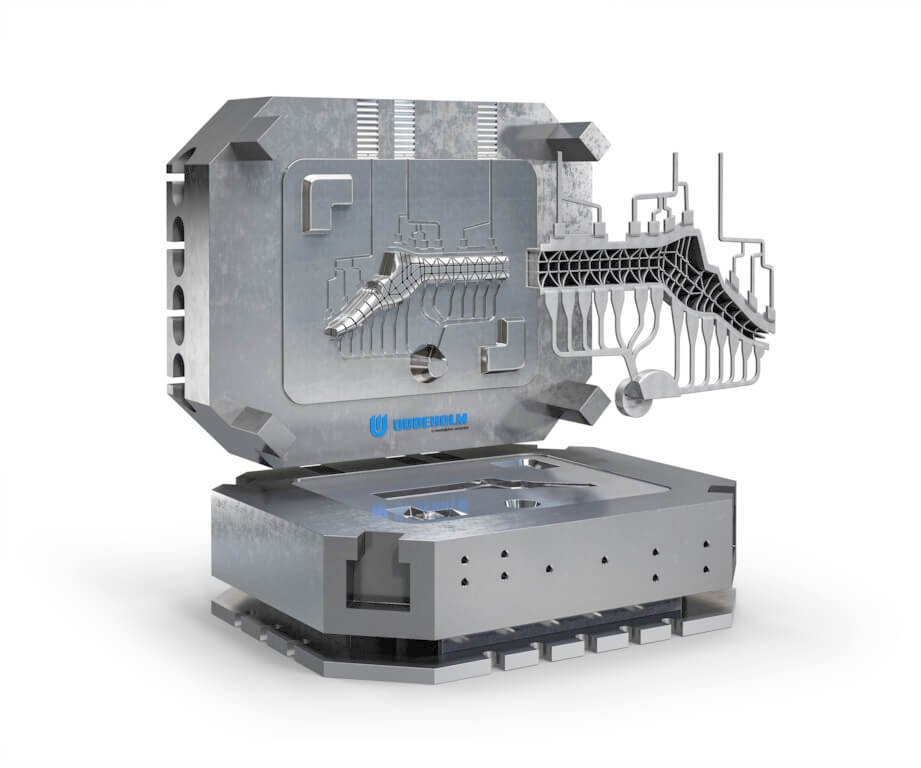
Auch seine Eignung als Schweißzusatzwerkstoff konnte Dievar unter Beweis stellen. Wie bei vielen anderen Sonderlegierungen bietet Uddeholm Schweißzusatzwerkstoffe aus Dievar an. Denn in bestimmten Fällen ist ein artgleicher Schweißzusatzwerkstoff notwendig oder sinnvoll. Neben den guten mechanisch-technologischen Eigenschaften zeigt sich, dass Dievar sehr gut schweißbar ist. Dievar Schweißzusatzwerkstoffe gibt es als MMA-Elektroden, MIG-Draht, WIG-Drähte und Drähte für das Laserschweißen.
Diese gute Schweißbarkeit ist eine wesentliche Eigenschaft, die zur Entwicklung von Dievar-Pulver für die additive Fertigung führte. Wir bieten Dievar-Pulver für das Pulverbettverfahren L-PBF (Pulvergröße 20-50 µm) und für das Laser Metal Deposition-Verfahren LMD (Pulvergröße 50-150 µm) an.
Teil 2 – Uddeholm Dievar – Laser Metal Deposition-Verfahren (LMD)
Neben dem Pulverbettverfahren spielt auch das Laser Metal Deposition (LMD) – Verfahren im Werkzeugbau bzw. den Gießereien eine Rolle. Beim LMD-Prozess wird
ein Bauteil oder der Bereich eines Bauteils über Laser-Pulverauftragsschweißen generiert. Aus unserer Sicht steht das LMD-Verfahren nicht im Wettbewerb zum
Pulverbett L-BF-Verfahren, da es eigene Möglichkeiten aufweist und damit andere Anwendungszwecke hat. Die Tabelle 1 unten gibt eine Übersicht über die Unterschiede beider Prozesse.
Pulverbett L-PBF | Laser Metal Deposition (LMD) | |
---|---|---|
Größe der Teile | Länge etwa 250 – 400 mm | Auch Längen > 1.500 mm möglich |
Designfreiheit | Können komplexe Geometrien mit inneren Strukturen hergestellt werden | Im Vergleich deutlich geringer |
Toleranzen | +/- 0,2 mm oder DIN 2768m | < 1mm |
Aufbau auf Grundkörper | Ausgangsfläche muss eben sein | Ausgangsfläche muss NICHT eben sein |
Aufbaurate | Gering | Hoch |
Verwendung unterschiedlicher Pulver | Nicht möglich in einem Bauprozess | möglich |
Oberflächenqualität nach „Drucken“ | Ra ~5–~30 µm (abhängig vom Bauwinkel) => Passflächen müssen zwingend nachbearbeitet werden, Angussbereiche ggf. nicht | Rz > 100 µm => Nacharbeit ist notwendig |
Aufgrund dieser Vorteile setzen wir das LMD-Verfahren zur Wiederinstandsetzung von Einsätzen ein. Auch diesbezüglich ist der LMD-Prozess als Ergänzung und nicht als Wettbewerb zu klassischen Schweißverfahren zu sehen. Der Aufwand für die Vorbereitungen ist höher als bei manuellen Schweißverfahren und damit ist der Prozess nicht so flexibel einsetzbar. Dafür ist beim LMD-Prozess die Qualität der Schweißung im Allgemeinen wesentlich höher und der Prozess reproduzierbarer (sh. Fakt 3). Nachstehendes Bild 5 zeigt die digitalisierte Prozesskette für die Wiederinstandsetzung von Einsätzen am voestalpine Additive Manufacturing Center in Düsseldorf.
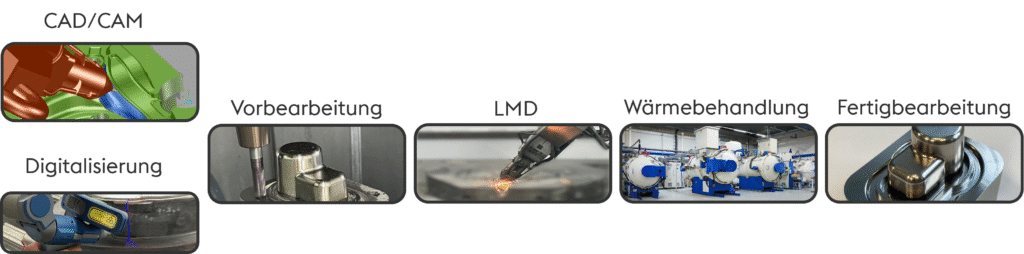
Fakt 3: Vorteile des LMD-Verfahrens gegenüber konventionellen Schweißverfahren:
> Geringe Wärmebeeinflusste Zone (WBZ); die WBZ ist eine der Hauptausfallursachen von Schweißungen
> Hochpräziser Werkstoffauftrag – Endkonturnahes Generieren
> Geringe thermische Belastung und dadurch geringerer Verzug
> Hohe Reproduzierbarkeit durch automatisierte und digitalisierte Prozesskette
> Materialmix möglich, da verschiedene Pulver verarbeitet werden können
Neben den verfahrenstechnologischen Vorteilen, die der LMD-Prozess bietet, darf die Werkstoffauswahl nicht vernachlässigt werden. Die voestalpine testet ihre Werkstoff- und Service-Lösungen für die Gießereitechnik meist in Zusammenarbeit mit dem Österreichischen Gießerei-Institut (ÖGI). So wurden auch Proben aus Uddeholm Dievar getestet, die durch das Laser Metal Deposition gefertigt wurden. Die Ergebnisse auf den Prüfständen bestätigen, dass die herausragenden Materialeigenschaften von Dievar auch bei der Verarbeitung im LMD-Prozess zum Tragen kommen. Insbesondere zeigte sich ein hoher Widerstand gegen thermische Ermüdung. Bild 6 fasst die Ergebnisse dieses Tests zusammen.
Werkstoffeigenschaften Prüfstandtestergebnisse vom ÖGI
(ÖGI – Österreichisches Gießerei-Institut)
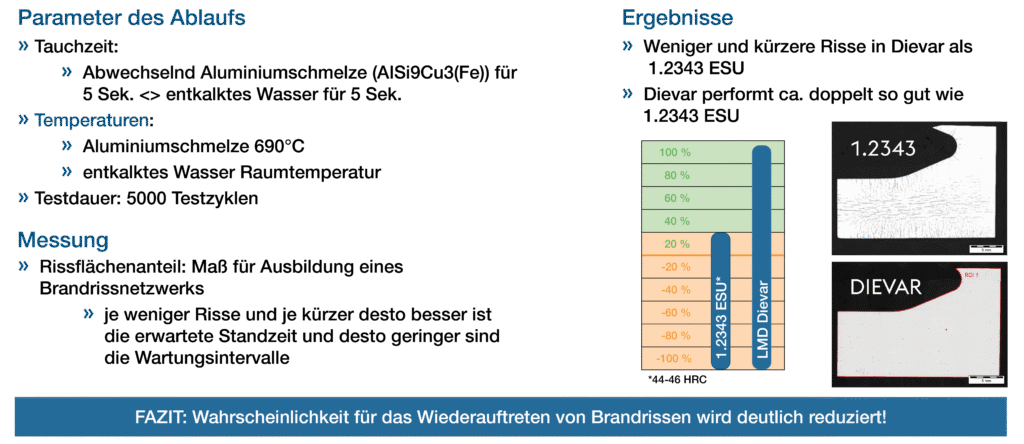
Bei der Prüfung wurden gekerbte Proben fünftausendmal abwechselnd in eine Aluminiumschmelze und in entkalktes Wasser getaucht. Es wurden Proben aus Uddeholm Dievar, die durch das Laser Metal Deposition gefertigt wurden, gegen Proben aus 1.2343 ESU (Stabstahl) getestet. Dievar (gefertigt im LMD-Prozess) zeigt einen wesentlich höheren Widerstand gegen thermische Ermüdung als 1.2343 ESU (Stabstahl).
Die Kombination aus den Möglichkeiten des LMD-Prozesses und der Verwendung des Warmarbeitsstahlpulvers Dievar ist unter anderem für folgende Fälle einer Wiederinstandsetzung ideal:
> Flächiges Wiederinstandsetzen von Formoberflächen, z.B. bei Brandrissen
> Wiederaufbau von Geometrien, wie Dichtnuten, Stege oder Domen
> Lokale Geometrieänderungen
Bild 7 unten zeigt den Kostenvorteil einer Wiederinstandsetzung gegenüber einer Neufertigung an zwei Beispielen von Einsätzen für den Aluminiumdruckguss.
Selbstverständlich können Sie als Gießer auch „nur“ das Dievar-Pulver für das Pulver-Laserauftragsschweißen kaufen. Wir möchten aber betonen, dass die Beherrschung der in Bild 5 beschriebenen Prozesskette aus unserer Sicht viel Erfahrung benötigt.
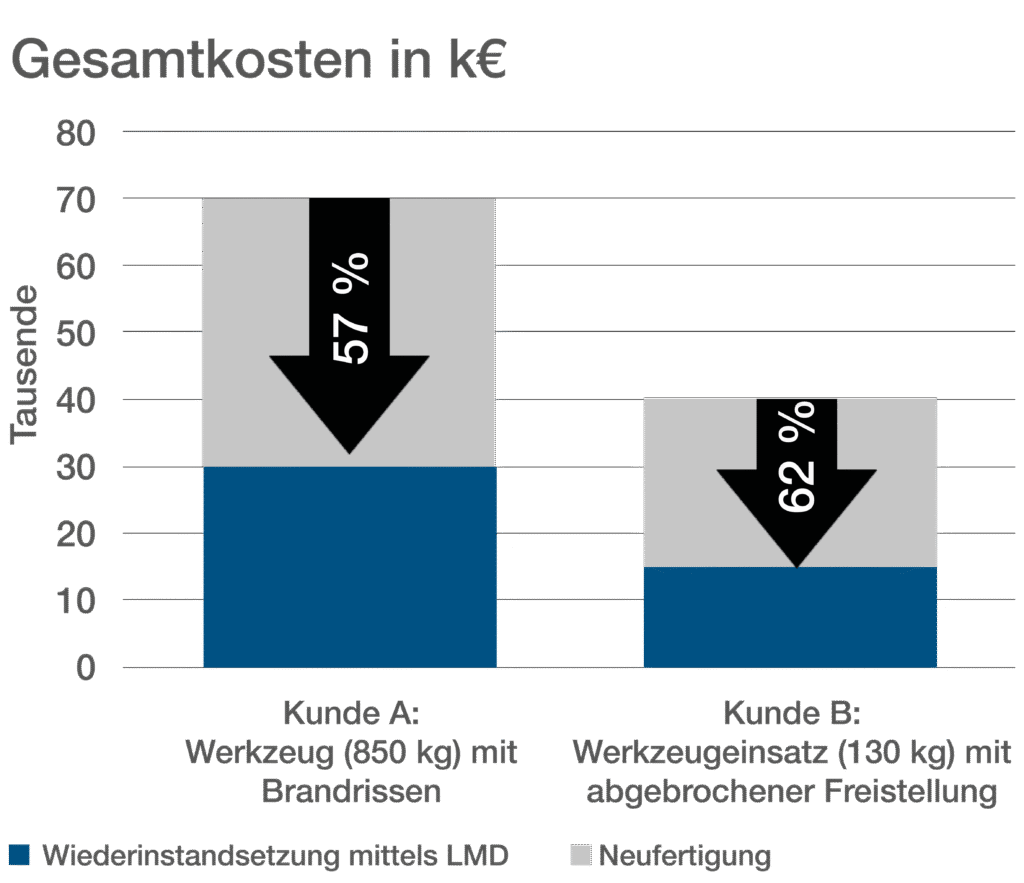
Ein Formeinsatz mit Stegen für Dichtnuten ist ein gutes Beispiel die Unterschiede zwischen dem Pulverbett L-PBF-Verfahren als Neuanfertigung und dem LMD-Prozess als Wiederinstandsetzung aufzuzeigen. Das grundsätzliche Problem beim Gießen von Dichtnuten ist, dass der Formeinsatz lange und dünne Stege aufweist, also Bereiche mit viel Oberfläche bezogen auf das Volumen. Dies hat zur Folge, dass sich die Stege nach dem Füllen der Kavität mit der Metallschmelze sehr schnell aufheizen und beim Sprühen schnell abkühlen. Dies führt aufgrund der Wärmeausdehnung zu hohen Spannungen in den Stegen und letztendlich zu Spannungsrissen. Wie oben beschrieben, kann man solchen Herausforderungen durch die Kombination von angepasstem Kühlkanaldesign und richtiger Werkstoffauswahl begegnen. Liegen die Kühlkanäle unter den Stegen – oder anders ausgedrückt, „folgen“ die Kühlkanäle den Stegen – wird die Temperatur dieser Stege kontrolliert. Dies bedeutet, dass der Thermoschock massiv reduziert wird und damit auch die resultierenden Spannungen.
Anwendungsbeispiel Gehäuse mit Dichtnuten
DAS PROBLEM DÜNNER STEGE
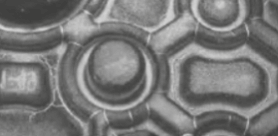
> Viel Oberfläche + wenig Volumen
> schnelle Temperaturänderungen = hohe Spannungen
> Häufig frühzeitiger Ausfall durch Rissbildung
DIE PROBLEMLÖSUNGSUNGEN
Refurbishing durch
Laser Metal Deposition (LMD)
Das
Das Problem an der Wurzel packen durch
Pulverbett L-PBF-Verfahren (AM Dievar)
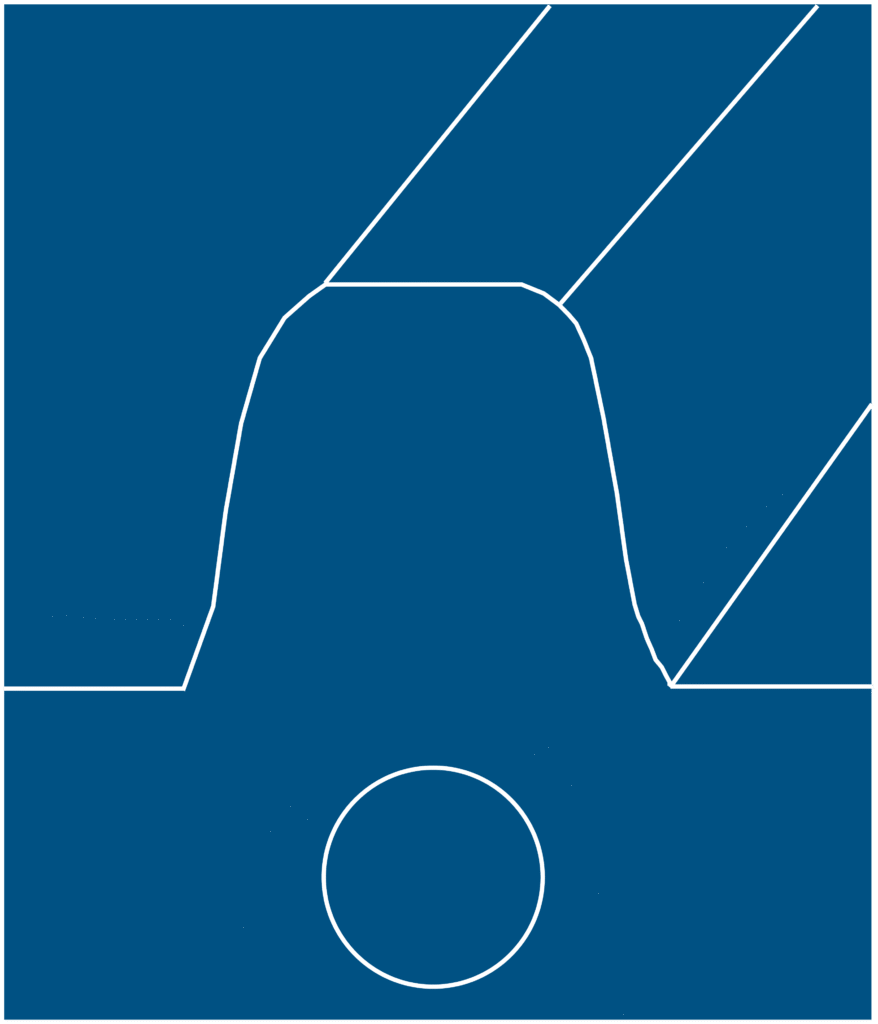
- Kühlung unterhalb des Stegs, dem Steg folgend durch Pulverbettverfahren
- Thermische Kontrolle + richtiger Stahl = weniger Risse
Vorteile: - Keine Nacharbeit der Dichtnut am Gussteil
- Standzeiterhöhung im Bsp. von 19.000 auf 48.000 Schuss mit AM Dievar
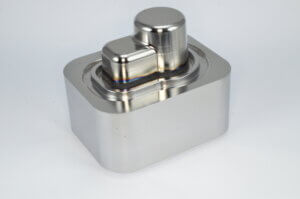
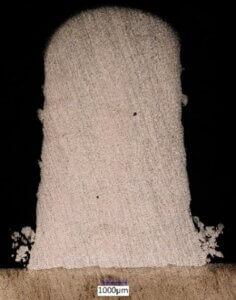
In einigen Fällen konnte das Reißen der Stege durch die Verwendung des L-PBF-Verfahrens sogar verhindert werden. Wenn aber die Stege zum Gießen von Dichtnuten Spannungsrisse aufweisen, die zu einer unzureichenden Bauteilqualität führen, muss man den Formeinsatz nicht verschrotten. Er kann durch das LMD-Verfahren wiederinstandgesetzt werden. Für beide Vorgehensweisen ist die Verwendung von Dievar-Pulver aufgrund seiner hohen Duktilität bei gleichzeitig hoher Warmfestigkeit verbunden mit der guten Verarbeitbarkeit ideal (sh. Bild 8).
Zusammenfassung
Die Gießereibranche steht vor der Herausforderung, dass die Anforderungen an die Gussteile steigen. Gleichzeitig müssen die Stückkosten gesenkt werden. Wesentliche Stellhebel für einen wirtschaftlichen Gießprozess sind unter anderem die Reduzierung der Ausschussrate, eine Erhöhung der Gesamtanlageneffektivität, höhere Standzeiten und eine Wiederinstandsetzung von Einsätzen. Das Zusammenspiel der Möglichkeiten der additiven Fertigung mit dem einzigartigen Eigenschaftsmix von Uddeholm Dievar kann zu deutlichen Produktivitätssteigerungen und Kosteneinsparungen in den Gießprozessen führen. Das Pulverbett L-PBF-Verfahren bietet eine hohe Designfreiheit, wodurch auch komplexe Geometrien mit inneren Strukturen hergestellt werden können. In den meisten Fällen wird dieses Verfahren für eine effiziente Temperierung der Formeinsätze verwendet. Das Laser Metal Deposition-Verfahren ist für die Wiederinstandsetzung von Formeinsätzen bestens geeignet.
In den Anfängen der additiven Fertigung für den Werkzeugbau stand bei der Pulverauswahl die Verarbeitbarkeit im Vordergrund. Daher wurden insbesondere im Pulverbettverfahren sogenannte ausscheidungshärtende Stähle verarbeitet. Heutzutage sollte aber aufgrund der hohen Anforderungen und Weiterentwicklungen in der additiven Fertigung der Fokus nicht auf der Verarbeitbarkeit, sondern auf die Leistungsfähigkeit in der Anwendung liegen. Uddeholm Dievar-Pulver für die additive Fertigung verfügt über die notwendigen Materialeigenschaften
Die Gießereibranche benötigt Partner, die innovative Lösungen anbieten und gleichzeitig den Gießprozess und seine Herausforderungen versteht. Die voestalpine High Performance Metals ist auf die Produktion und Verarbeitung von Hochleistungswerkstoffen und kundenspezifische Services fokussiert. Wir sind globaler Marktführer bei Werkzeugstahl. Unsere weltweite und langjährige enge Zusammenarbeit mit unseren Kunden führt zu anwendungsspezifischen Services.
Das Uddeholm Dievar-Pulver für die additive Fertigung als Produkt sowie seine Verarbeitung im Pulverbett L-PBF-Verfahren oder im Laser Metal Deposition–Verfahren zu gebrauchsfertigen Teilen sind ein Beispiel für unsere innovativen Lösungen für die Gießereibranche, um die Kosten pro Gussteil zu senken!
Nehmen Sie Kontakt mit uns auf und fordern Sie uns heraus!