Teil 1 – Uddeholm Dievar
Pulver für die additive Fertigung
Uddeholm Dievar ist ein etablierter Warmarbeitsstahl. Seine erstklassige Kombination aus Zähigkeit und Warmfestigkeit führt in vielen Fällen zu deutlich längeren Standzeiten. Seit einigen Jahren ist Dievar auch als Pulver für die additive Fertigung verfügbar. Das Zusammenspiel der Möglichkeiten der additiven Fertigung mit dem einzigartigen Eigenschaftsmix von Dievar kann zu deutlichen Produktivitätssteigerungen und Kosteneinsparungen im Druckgießprozess führen.
Uddeholm Dievar als erprobter Warmarbeitsstahl wird weltweit vor allem für Druckgussformen eingesetzt. Er bietet eine herausragende Zähigkeit, Warmfestigkeit und Einhärtbarkeit. Insbesondere beim Gießen von Strukturteilen kommen die Vorteile dieses Eigenschaftsmix zum Tragen. Damit trägt der Trend zu gegossenen Strukturteilen aus Aluminium zum Erfolg von Dievar bei. Ein Meilenstein in der „Vita“ von Dievar war die Erhöhung der garantierten Kerbschlagbiegearbeit von 19 auf 25 Joule (Charpy-V Werte nach Lieferrichtlinie NADCA #207; „Capability“). Durch Optimierungen in der Stahlherstellung konnte die Zähigkeit insbesondere bei großen Abmessungen gesteigert werden.
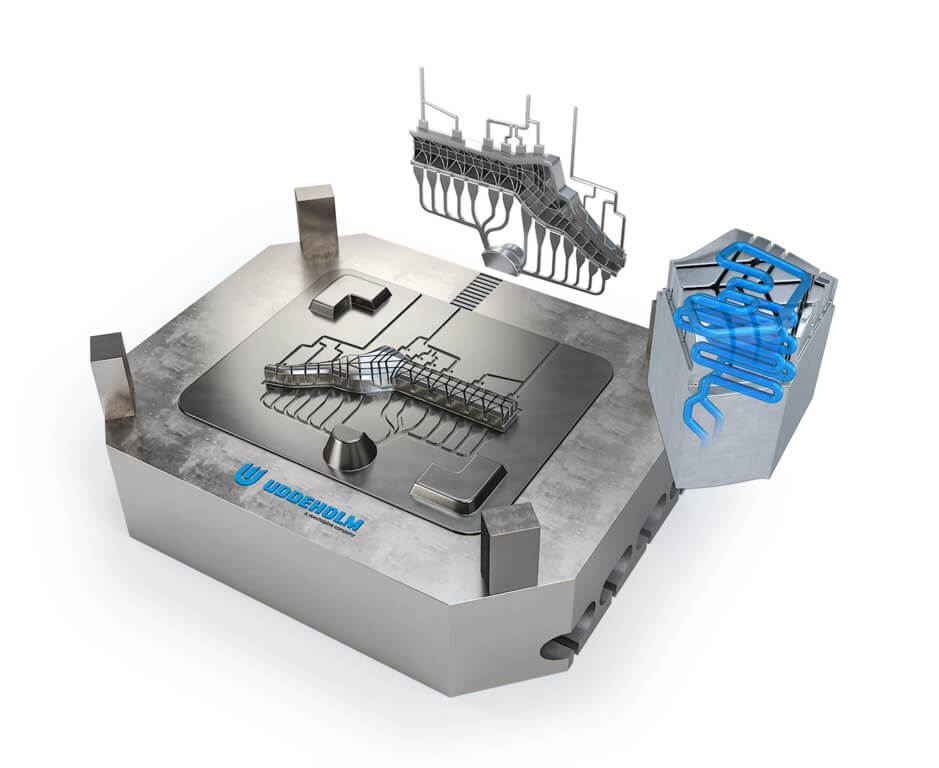
Diesen Vorteil geben wir an unsere Kunden durch erhöhte Garantien weiter. Damit nimmt Uddeholm Dievar eine einzigartige Stellung unter den Warmarbeitsstählen ein. Dieses wird unter anderem dadurch sichtbar, dass er in der Kategorie „Typ C1850“ in der NADCA #207 eingeordnet ist. In dieser Kategorie sind die Warmarbeitsstähle mit einer hohen Warmfestigkeit (2,0 – 3,3 Gew.-% Molybdän) und gleichzeitig hohen Zähigkeit (mindestens 25 Joule Kerbschlagbiegearbeit nach Lieferrichtlinie NADCA #207; „Capability“) aufgelistet.
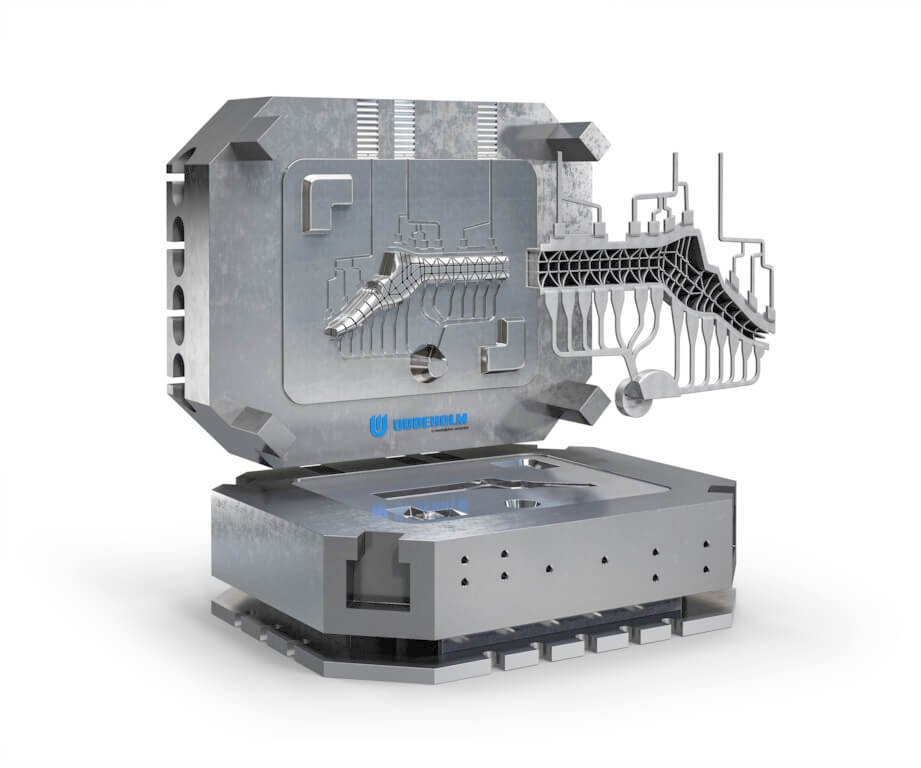
Auch seine Eignung als Schweißzusatzwerkstoff konnte Dievar unter Beweis stellen. Wie bei vielen anderen Sonderlegierungen bietet Uddeholm Schweißzusatzwerkstoffe aus Dievar an. Denn in bestimmten Fällen ist ein artgleicher Schweißzusatzwerkstoff notwendig oder sinnvoll. Neben den guten mechanisch-technologischen Eigenschaften zeigt sich, dass Dievar sehr gut schweißbar ist. Dievar Schweißzusatzwerkstoffe gibt es als MMA-Elektroden, MIG-Draht, WIG-Drähte und Drähte für das Laserschweißen.
Diese gute Schweißbarkeit ist eine wesentliche Eigenschaft, die zur Entwicklung von Dievar-Pulver für die additive Fertigung führte. Wir bieten Dievar-Pulver für das Pulverbettverfahren L-PBF (Pulvergröße 20-50 µm) und für das Laser Metal Deposition-Verfahren LMD (Pulvergröße 50-150 µm) an.
Für Einsätze für Druckgusswerkzeuge hat sich unter den additiven Verfahren das Pulverbettverfahren L-PBF etabliert. In bestimmten Fällen ist eine wirtschaftliche Herstellung von Aluminiumdruckgussteilen ohne diese Technologie nicht mehr möglich. Das Pulverbettverfahren bietet eine hohe Designfreiheit und Genauigkeit, wodurch komplexe Geometrien mit inneren Strukturen hergestellt werden können.
Uddeholm Dievar – Pulverbettverfahren L-PBF
In den meisten Fällen wird dieses Verfahren für eine effiziente Temperierung der Einsätze verwendet.
Additiv gefertigte Einsätze für den Druckguss werden teilweise leider noch aus 1.2709 -Pulver gedruckt. Und dies nicht wegen der guten Performance im Gießprozess, sondern wegen der guten „Druckbarkeit“. Der nickellegierte Maragingstahl 1.2709 hat aber im Druckguss gravierende Nachteile (sh. Fakt 1). Hervorzuheben ist, dass die Zähigkeit von Uddeholm Dievar aus der additiven Fertigung höher ist als bei Dievar-Stabstahl. Und Dievar-Stabstahl ist wesentlich zäher als Standard-Premium-Warmarbeitsstähle wie 1.2343 ESU. Da Dievar als Pulver und Stabstahl verfügbar ist, ist die Fertigung von hybriden Bauteilen aus Dievar kein Problem. Unter einer hybriden Fertigung versteht man den additiven Aufbau von Strukturen auf bereits bestehenden Halbzeugen, die konventionell gefertigt wurden. Dadurch können Fertigungskosten deutlich gesenkt werden – sh. Bild 1.
Oben – Additiv gefertigter Bereich:
I.d.R. der Konturbereich, wo durch einen dreidimensionalen Verlauf der Kühlkanäle eine
optimale Temperierung erzielt wird.
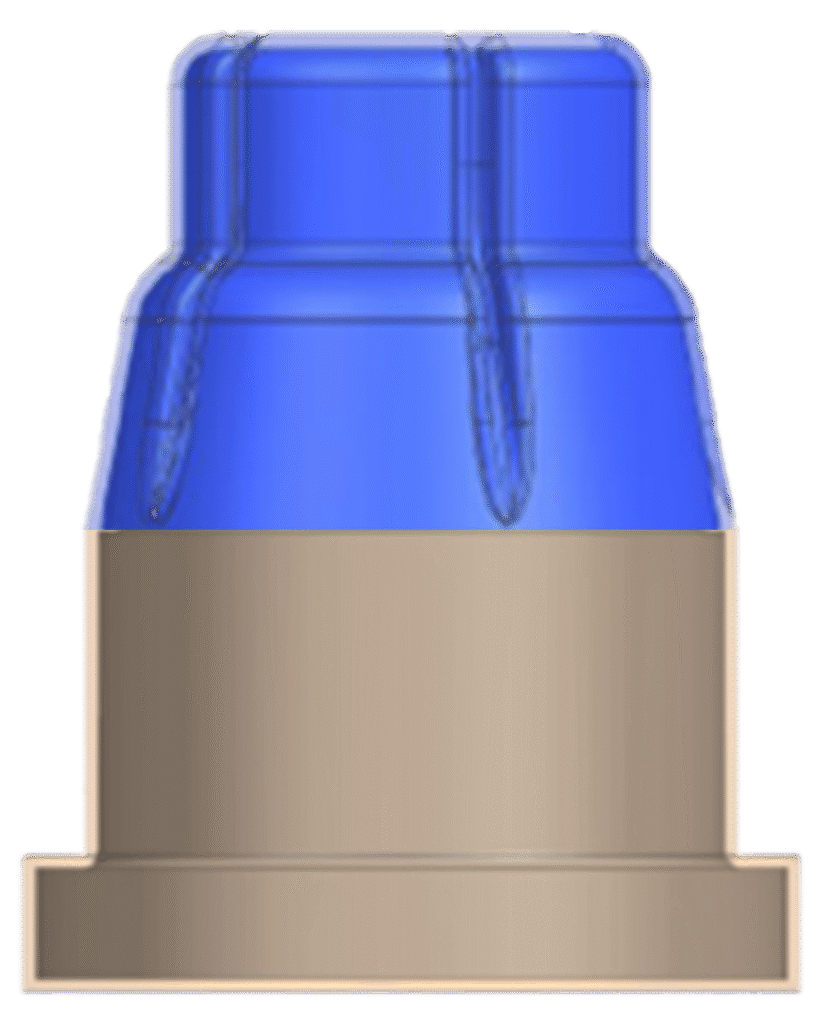
Unten – Konventionell gefertigter Bereich:
Der Bereich, wo die Geometrie bzw. die Kühlkanäle konventionell gefertigt werden. Hier bietet die additive Fertigung keine Vorteile und es können Kosten reduziert werden.
Fakt 1 – Vorteile von additiv gefertigten Bauteilen aus Dievar gegenüber 1.2709
> Deutlich höhere Zähigkeit (Zähigkeit ist sogar höher als Dievar Stabstahl)
> Deutlich höherer Widerstand gegen Metallkorrosion (Ni-freier „normaler“ Warmarbeitsstahl)
> Höhere Wärmeleitfähigkeit (29,4 W/mK bei 400 °C)
> Stabile Eigenschaften, da keine Gefügeumwandlung in Austenit bei hohen Temperaturen
> Co-frei
Wichtig für Sie als Gießerei ist, dass wir als voestalpine Ihnen die komplette Fertigungstiefe anbieten können. Besitzen Sie einen eigenen Drucker, liefern wir Ihnen „nur“ das Dievar-Pulver. Möchten Sie das Bauteil selbst auslegen und designen, führen wir das Lohndrucken inklusive der Wärmebehandlung durch. Design und Simulation bieten wir ebenfalls an.
Wenn Sie es wünschen, fertigen wir ein einsatzfertiges Bauteil, das heißt inklusive mechanische Bearbeitung und gegebenenfalls Oberflächenbehandlung (Polieren, PVD-Beschichtung, Texturierung, Nitrierung, etc.) – sh. Bild 2.

Die Auslegung der Temperierung erfordert entsprechendes Wissen und Erfahrung. Unsere Marktanalysen zeigen, dass die hohe Designfreiheit auch leicht zu einem ungeeigneten Kühlkanaldesign führen kann. In den meisten Fällen wünschen die Kunden daher, dass wir auch das Design und die Simulation ausführen. Denn wir kennen und verstehen sowohl den Gießprozess als auch die additive Fertigung. Durch unsere langjährige Erfahrung haben wir uns diesbezüglich ein umfangreiches Know-How aufgebaut und verwenden dafür geeignete Design- und Simulations-Software.
Oft hört man von Gießereien den Satz: „Die additive Fertigung von Einsätzen ist mir zu teuer“. Betrachten wir diese Aussage unter zwei Aspekten:
Aspekt 1: Vergleich der Beschaffungskosten eines Einsatzes
In vielen Fällen sind additiv gefertigte Einsätze teurer als konventionell gefertigte Einsätze. Zu berücksichtigen ist jedoch, dass der Kostenunterschied von additiv gefertigten Bauteilen zu konventionell gefertigten Bauteilen von der Komplexität des Bauteils abhängt. Je komplexer das Bauteil, desto günstiger ist im Vergleich die additive Fertigung, da hier die Komplexität keinen Einfluss auf die Kosten hat. In bestimmten Fällen ist die additive Fertigung sogar günstiger, besonders wenn es sehr aufwendige konventionell gefertigte Kühllösungen sind (sh. Bild 4 rechts).
Aspekt 2: Vergleich der Kosten pro gegossenes Teil
Bei der Verwendung von additiv gefertigten Einsätzen sollte man wie bei jeder Technologie verstehen, welchen Nutzen man durch die Verwendung erzielen will. Will man z.B. die Zykluszeit verkürzen, die Gesamtanlageneffektivität erhöhen, die Ausschussrate senken oder die Standzeit des Einsatzes erhöhen. Bei der Betrachtung ist es wichtig, die Kostenstruktur des gegossenen Teils und insbesondere die „verborgenen Kostenfallen“, z.B. ungeplante Maschinenstillstandzeiten zu kennen (sh. Fakt 2). Am Ende sollen die Kosten pro gegossenes Teil gesenkt werden. Mit unserem Kalkulationstool können wir Sie hierbei gerne unterstützen. Unsere Erfahrungen zeigen, dass sich auch höhere Investitionen in die Form schnell amortisieren können und am Ende ist oft auch der „Experte“ überrascht, welche Kosteneinsparungen möglich sind.
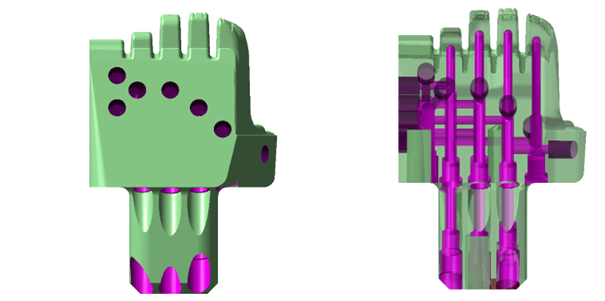
Fakt 2 – Kostenarten am gegossenen Bauteil, die durch das Werkzeug beeinflusst werden:
> Werkzeugkosten: Anschaffungskosten pro Form bzw. Einsatz
> Standzeit der Form: Bestimmt die Anzahl der benötigten Einsätze bzw. Formen für das Projekt
> Zykluszeit
> Maschinenstillstandzeiten (u.a. für Reparatur & Wartung, Anfahren, Werkzeugreinigung, …)
> Ausschussrate
> Kosten für Reparatur und Instandhaltung der Form
> Kosten für Nacharbeit („Putzen“) des Gussteils
Betrachten wir ein konkretes Beispiel, wo folgende Ausgangsbedingungen vorlagen:
> Maschinenstundensatz der Druckgussmaschine: 295 € pro Stunde
> Durchschnittliche Anlagenverfügbarkeit: 77 %
> Reinigungsaufwand aufgrund von „Belagbildung“: ca. 21 Minuten pro Schicht
> Zykluszeit: 73 Sekunden
> Ausschussrate: 8,2 %
> Benötigte Gussteile für das Projekt: 450.000 Gussteile
Es wurde ein additiv gefertigter Einsatz mit konturnaher Kühlung in den Schieber eingebaut. Die zusätzlichen Kosten betrugen 3.902 € pro Schieber beziehungsweise
39.020 € für das Projekt, da 10 Schieber benötigt wurden.
Durch die Verwendung der additiv gefertigten Einsätze wurden folgende Optimierungen erreicht:
- Ausschussrate sank von 8,2 % auf 3,9 % => Einsparung von 166.410 €;
ca. 37 Cent pro Gussteil - Aufgrund der niedrigeren Oberflächentemperatur bildete sich am additiv gefertigten Einsatz kein „Belag“.
In anderen Bereichen musste aber „Belag“ entfernt werden. Der Zeitaufwand sank auf ca. 7 Minuten pro Schicht => Einsparung von 40.500 €; ca. 0,09 € pro Bauteil
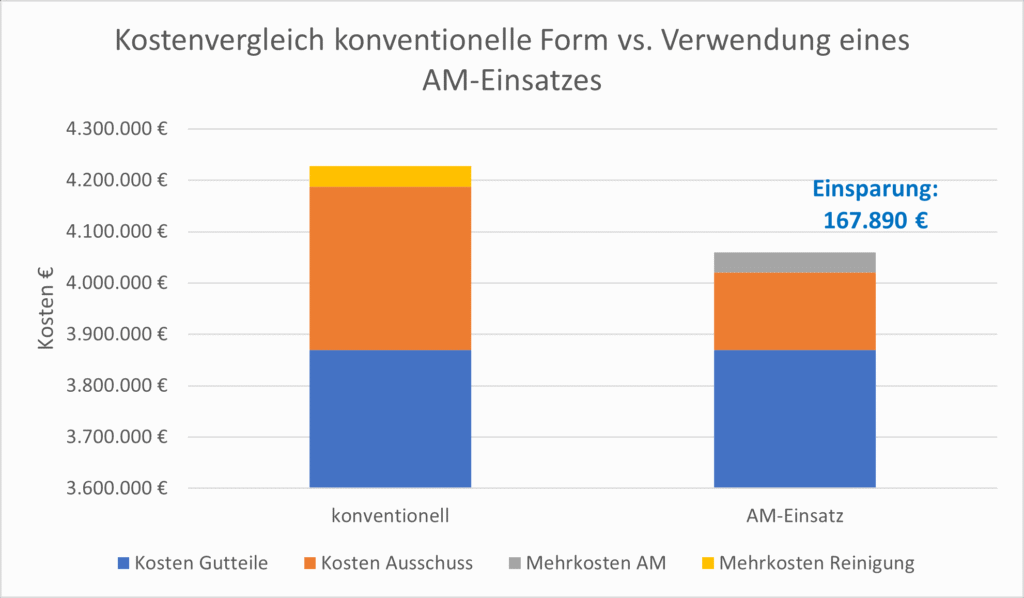
Neben dem Pulverbettverfahren spielt auch das Laser Metal Deposition (LMD) – Verfahren im Werkzeugbau bzw. den Gießereien eine Rolle. Beim LMD-Prozess wird
ein Bauteil oder der Bereich eines Bauteils über Laser-Pulverauftragsschweißen generiert. Aus unserer Sicht steht das LMD-Verfahren nicht im Wettbewerb zum
Pulverbett L-BF-Verfahren, da es eigene Möglichkeiten aufweist und damit andere Anwendungszwecke hat. Die Tabelle 1 unten gibt eine Übersicht über die Unterschiede beider Prozesse.