Hot Stamping
Hot stamping has rapidly become a complement to cold forming in the automotive industry – and no wonder. By using a heated blank that forms and hardens quickly in the die, parts can be made larger, stronger and more complex than ever before.
This means fewer structural parts per vehicle, to the tune of 30-35% weight reduction of individual parts. Naturally, this places severe demands on the tool steel used in the dies. For instance, to function reliably at the temperatures involved in the tool steel, it needs to have excellent thermal conductivity and hot yield strength as well as high toughness and ductility.
Hot stamping already means a great advantage over traditional production methods. By choosing the right tool steel you can maximize this advantage. With steel from Uddeholm, it is possible to avoid common problems and go straight for longer, more predictable, production runs and reduced cycle times.
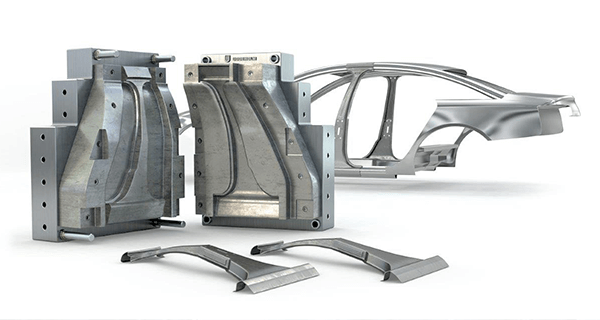