The quest for higher quality and more efficient production is a continued struggle for most industries but for the plastic injection molding process that requires big investments, both in molding equipment and in tools, so it is crucial to have high productivity to bear the costs for these investments. The limiting factor for the productivity is often the cooling time for the molded parts before ejection from the mold, and that sets the cycle time to produce the part and the productivity.
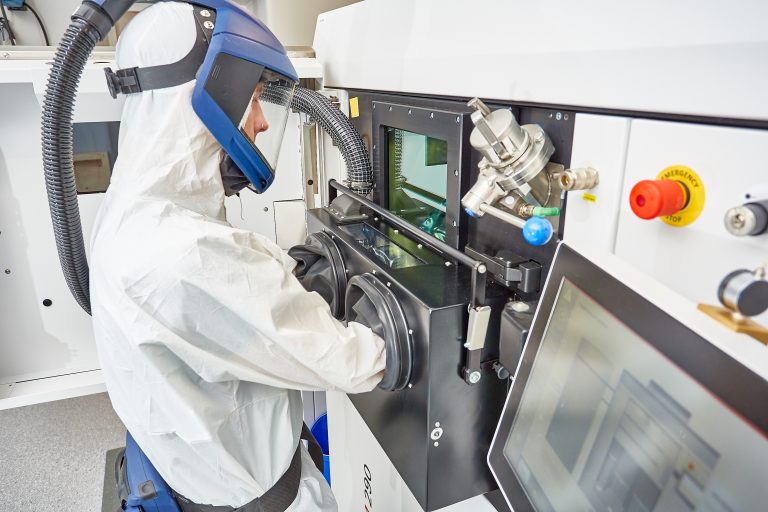
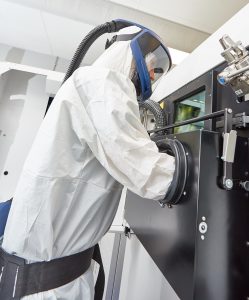
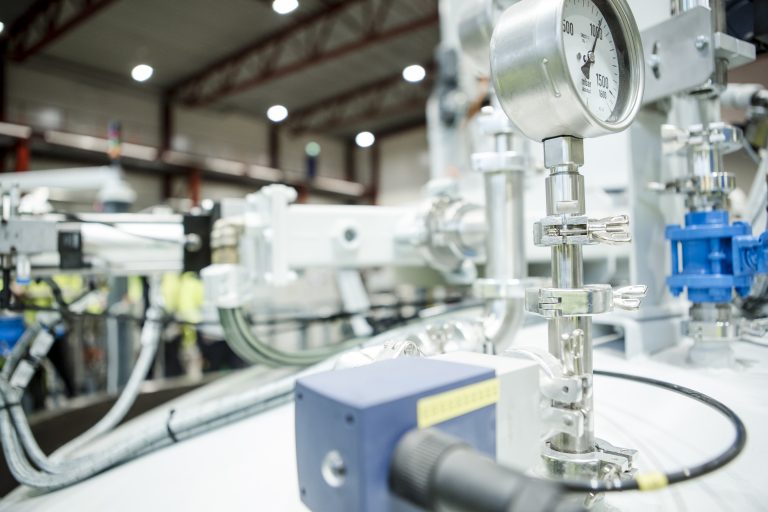
A lot of effort is put to reduce the cycle time and one popular way is to use mold materials with high thermal conductivity to speed up the heat transfer and cool the molded parts quicker. So injection molders turn to for instance aluminium or beryllium copper for the molds and dies instead of the traditional tool steel to benefit from the up to 10 times better thermal conductivity of these materials to decrease the cycle time and increase productivity. Using these materials with high thermal conductivity has proven an efficient way to lower the cycle time but these materials also have some disadvantages compared to the traditional tool steel. The hardness and strength of the aluminium mold materials are lower than for tool steel, which leads to wear of the tool, or even worse cracking, that can limit the lifetime of the tool.
When using beryllium copper can the strength and hardness often be sufficient for the tools but there are environmental and especially health issues with the beryllium copper so that it during die manufacturing or processing can be harmful for the operators and persons in contact with the mold. The health issues caused by the beryllium copper can and should avoided but that also leads to more complex and costly mold manufacturing.
But there is now new options to reduce the cycle time in plastic injection molding by making tools and dies by additive manufacturing. This technology gives new possibilities when it comes to producing complex geometries and for plastic injection molders that is especially interesting when designing the cooling system of your molds.